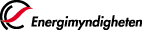
Husguiden
Börja med energismarta vanor
Gör en husesyn
Minska behovet av värme och varmvatten
Se över husets uppvärmning
Ta ditt hus till nästa nivå
När du ska anlita hantverkare
Så mycket kan du spara på att effektivisera ditt hus
Jag vill energieffektivisera mitt företag
Företagsguiden - för dig som vill energieffektivisera ditt företag
Ekonomiska stöd och rådgivning
Energikartläggning
Vägledning och hjälp
Inköp av produkter
Hitta din energi- och klimatrådgivare
Nätverk och beställargrupper
Jag vill energieffektivisera hemma
Spara energi - enkla tips
När du ska köpa nya produkter
Energi- och klimatrådgivning
Anlita en certifierad installatör
Anmäl en bristfällig produkt
Energieffektivisering inom offentlig sektor
Arbeta strategiskt med energieffektivisering
Spara energi genom beteendeförändringar
Tekniska åtgärder för lokaler
Åtgärder för övriga lokaler
Spara energi på arbetsplatsen
Mervärden av energieffektivisering
Aktörer som bidrar med kunskap och goda exempel
Energieffektivisering för flerbostadshus
Dialog med boende
Driftåtgärder
Tekniska åtgärder som kräver större investeringar
Jag arbetar med energieffektivisering
Energikonsult
Byggbranschen
Installatör
Energi- och klimatrådgivare
Energimyndighetens stöd
Jag är säljare eller tillverkare av produkter
EPREL - Europeisk databas för energimärkta produkter
Ekodesign, energimärkning och CE-märkning
Marknadskontroll av produkter
Produktgrupper A-Ö
Skyldigheter och ansvar
Nyhetsbrev
Aktuella möten och konsultationer
Tester
Energimyndighetens Testlab
Belysningstester
Hemelektroniktester
Tester inom solenergi
Tester om uppvärmning och varmvatten
Tester hushållsapparater
Tester A-Ö
Forskningsområden
Bebyggelse
Bioenergi
Energiriktad grundforskning
Elsystem
Energisystemen i samhället
Industri
Internationella insatser
Impact Innovation
Kompetenscentrum
Strategiska innovationsprogram
Transporter
Värme och kyla
Solelportalen
Har mitt hus rätt förutsättningar?
Hur stor anläggning passar mig?
Vilka stöd och intäkter kan jag få?
Vad kostar det?
Vad ska jag tänka på vid inköp och val av leverantör?
Rättigheter och skyldigheter vid installation
Drift och underhåll av din solcellsanläggning
Att tänka på vid avveckling eller flytt
Kom i kontakt med lokal energi- och klimatrådgivare
Om solelportalen
Elproduktion
Solenergi
Vattenkraft
Vindkraft
Lokala och regionala insatser för förnybar elproduktion
Internationella klimatsamarbeten
Parisavtalet
Kyotoprotokollet
FN:s klimatmöte COP
Rapporter och analyser
Frågor och svar om internationella klimatsamarbeten
Handel med utsläppsrätter
Nyheter
Om utsläppshandel
För dig som vill handla eller är verksamhetsutövare
Officiell energistatistik
Användningsvillkor
Enheter och symboler
Om den officiella statistiken
Publiceringsplan 2024
Användarråd för officiell statistik
Statistikdatabas
Fakta om energiläget
Goda förutsättningar inför vintern
Faktorer som påverkar elpriserna
Sveriges energiläge
Uppföljning av elanvändning
El och Fjärrvärme
Elenergibrist
Eleffektbrist
Elavbrott
Styrel
Fjärrvärme
Riskberedskap inom elsektorn
Olja och drivmedel
Kartläggning av drivmedelsbehov
Beredskapslagring av olja
Frågor och svar om lageravtappning
Naturgas
Västsvenska naturgasnätet
Gasnätet i Stockholmsområdet
Övriga nät, tankställen och LNG-terminaler
Gasprisstöd
El-, gas- eller fjärrvärmeavbrott
Tips – så bor du kvar vid ett längre värmeavbrott
Checklista – dessa prylar behöver du
Inget vatten i kranen – så förbereder du dig
Laga mat utan el eller gas – så gör du det säkert
Fem enkla råd för att hålla värmen
Reservelverk & reservvärme
Quiz: Testa dig – är du tillräckligt förberedd?
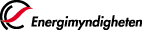